DTP
The Master of Depuration
for the Glass Industry
The DTP is a unique and exclusive system that provides PURIFIED WATER through a combination of a physical-dynamic separation accelerator and a microfiltration process. This is indeed its name according to the dictates of physics; however, DTP is the product brand that encapsulates this definition in the acronym for Technical Deconcentration under Pressure.
This characteristic allows for real-time return of as much purified water to the machines as they require for their operation (see QUALITY OF PURIFIED WATER section), bypassing the pumps of the machines themselves, without interruptions in continuity, without intermediate pumping stations, and without interruptions in the closed pressurized circuit. The DTP provides, in a single output, its entire nominal capacity of water, all treated and purified, and with the aforementioned quality parameters (see MICRO FILTRATION).
The DTP is easily configurable in the numerous available sizes, with each designation indicating the nominal purification capacity in cubic meters per hour, corresponding to the quantity of purified water delivered to the machines in one hour.
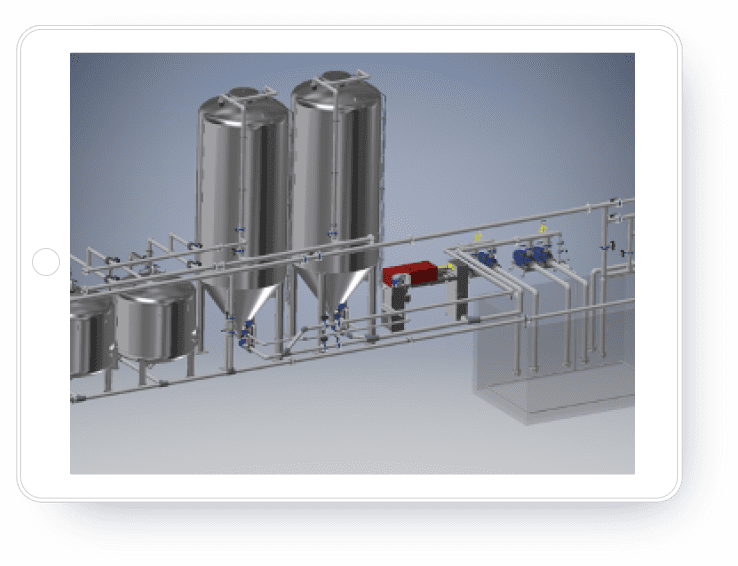
THE WATER FILTRATION PROCESS
WATER COLLECTION
The dirty water resulting from processing flows through drainage channels into a common collection tank. It is possible to return the dirty water by pumping it directly from the machines or from remote sumps.
An initial pre-filtration in a small sump will separate foreign materials (such as cigarettes, wood, polystyrene, etc.) and large glass fragments. After passing through the pre-filtration sump, the water will flow into the collection tank.
At the bottom of the collection tank, a fluidization ring is installed, consisting of various water jets powered by the same pump responsible for pushing the water into the purification circuit (see section PUMPING STATION). Its function is to prevent sludge from settling at the corners and bottom of the tank, ensuring continuous and automatic cleaning without the need for maintenance and descaling.
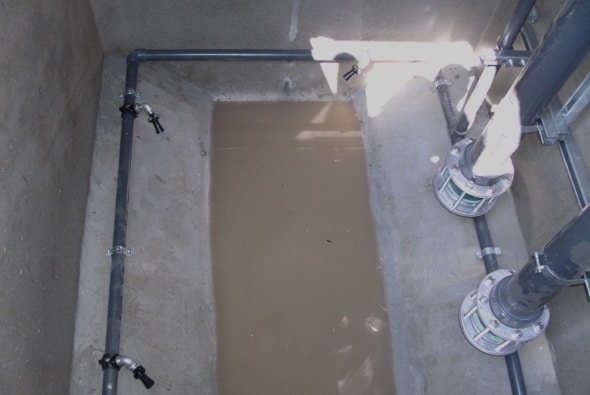
PUMPING STATION
Two identical pumps operate alternately on a daily cycle, drawing water from the collection tank and pressurizing it through the treatment plant. Thus, the system will always operate with only one pump running at a time.
Each pump is installed with its own check valve at the beginning of its suction line. An anti-cavitation system is in place.
As described in the previous section, a small portion of the water flow, driven by the same pump in operation, returns to the original tank to constantly feed the fluidization circuit.
From the pumping station onward, the entire DTP system and circuit are filled with water and operate completely under pressure without interruption. The pressure is provided by the initial pump and is maintained up to the machineries.
Several sensors (both visual and electronic) monitor the pump’s operation, pressure, and water flow, sending their information to the central system for automated flow management and pump power regulation via an inverter, ensuring the stability of the set working pressure.

DECONCENTRATOR
The Deconcentrator is the main unit where the physical-dynamic separation between water and sludge occurs.
The dirty water, pumped in, enters the Deconcentrator through a small central inlet in the lower cone and exits, purified, from the lateral outlets at the top.
Inside the Deconcentrator, the water undergoes a specific movement that, through particular dynamics, separates the suspended solids from the water particles.
The glass sludge automatically remains in the two chambers at the lower part of the Deconcentrator, while the clear water exits from the top of the Deconcentrator to reach the next stage of filtration.
The sludge (water with a very high concentration of residue) is automatically discharged from the Deconcentrator through the regular opening of two pneumatic valves (see section SLUDGE DISCHARGE).
The sequence of these sludge discharge openings occurs automatically at regular intervals, integrated with data from flow meters.
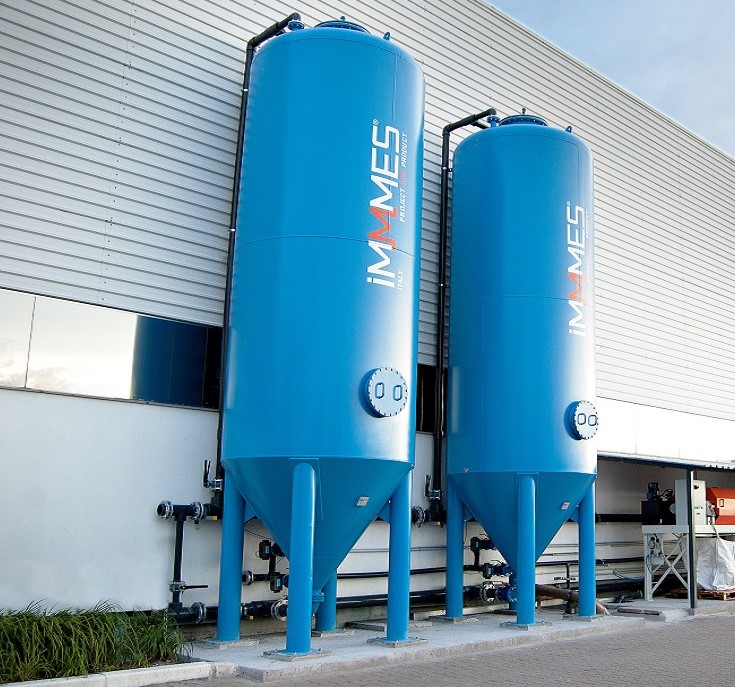
FILTRATION
After exiting the top of the Deconcentrator, the water arrives at the filter where, driven by the initial pressure, it passes through a traditional multi-mineral filter.
The quality of filtration falls under the category of MICRO FILTRATION. Individual residual particles are less than 5 microns in size, and the total residual PPM is less than 2 mg/litre. The water appears CLEAR.
After filtration, all purified water flows directly to the machineries through existing distribution lines (maintaining pressure from the initial pump).
The filter self-cleans on a daily basis. Therefore, it requires no maintenance or replacement of the filter bed. This operation takes approximately 35-40 minutes and typically occurs overnight or at the most convenient time for the client (it automatically starts based on the preset schedule, including weekends and holidays).
The combination of various valves at the filter inlet (Multi-circuit System) allows the system to automatically manage these modes: OPERATION – BACKWASH – RINSE – BYPASS (the latter only in safety mode).
Inside the filter, two metal dividers (upper and lower) with numerous holes are installed for specific micro-filter installation. Each micro-filter retains sands and filtering stones inside the filter, allowing only purified water to pass through. This ensures that sands and minerals remain inside the filter indefinitely without needing replacement.
During the backwash phase, dirty water discharged from the filter returns to the collection tank.
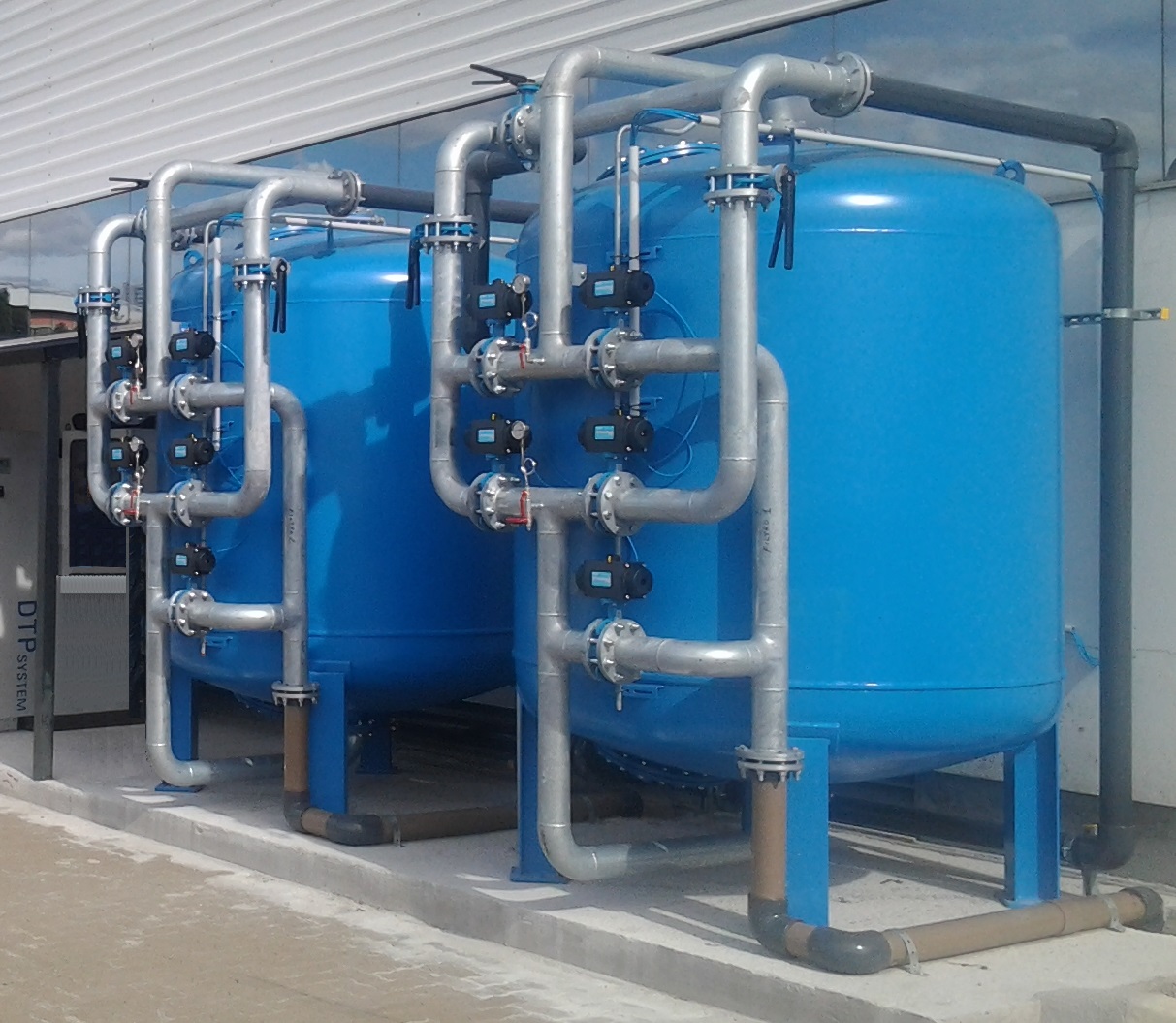
SLUDGE DISCHARGE AND TREATMENT (from the Deconcentrator)
Directly from the two outlets located at the bottom of the Deconcentrator, the sludge is expelled to the Filter Press station (or alternatively to the Big Bags). The Filter Press (which is part of the DGS product line) is available as an option in smaller plants, while for plants starting from 50 m³/hour, it is provided as standard.
In smaller plants, while the Filtropress installation is always possible, a bag filter station (known as Big Bags) is typically offered as standard. Depending on the plant size, the number of filter bags can range from a minimum of 3 up to 12.
Big Bags filter water, retaining the solid part (sludge) inside the sack and filtering the cleaned water into the base basin, which then returns to the initial tank via gravity.
The removal of full Big Bags, filled with solidified sludge, is done using a simple pallet jack. New filter bags are then installed to continue the filtration process.
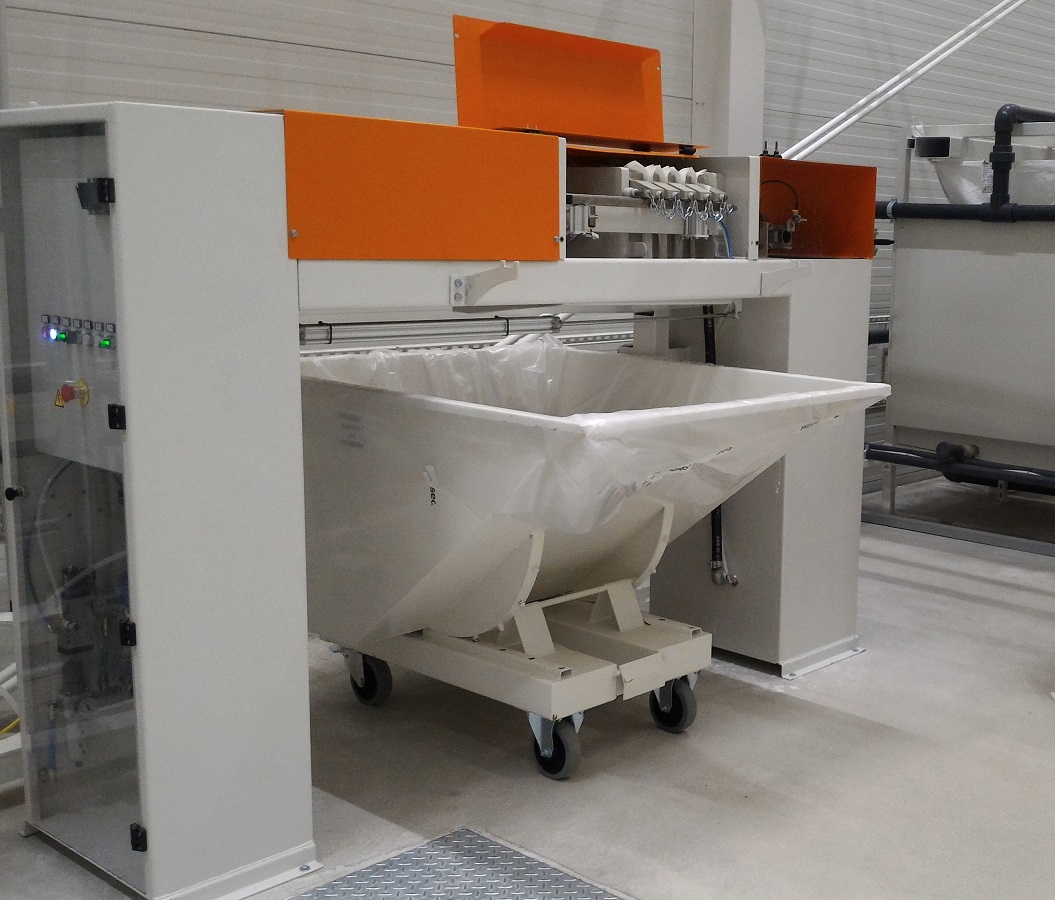
ELECTRICAL PANEL AND CONTROLS
Each function is guaranteed to operate in automatic or manual mode. The normal operation of the system is in fully automatic mode, handling all necessary functions for factory service without the need for operator intervention.
Located on the front panel of the control board are all the controls enabling these modes for each individual function.
A PLC (Programmable Logic Controller), equipped with touch-screen functionality, manages the parameters and control of the system. Our proprietary software is divided into various menus and submenus to facilitate data management and reading. The DTP can be equipped with additional software packages for remote control and integration with other processing machines.
The working pump is controlled by an inverter that ensures proper electrical supply based on the required flow from the factory.
A central memory records every signal or alarm, and a flashing light or siren activates in case of any anomaly (programming is user-settable).
The DTP allows Remote Monitoring via an IP protocol for Immmes’ after-sales service. Additionally, a Remote Control option is provided for client control (factory manager/owner, etc.).
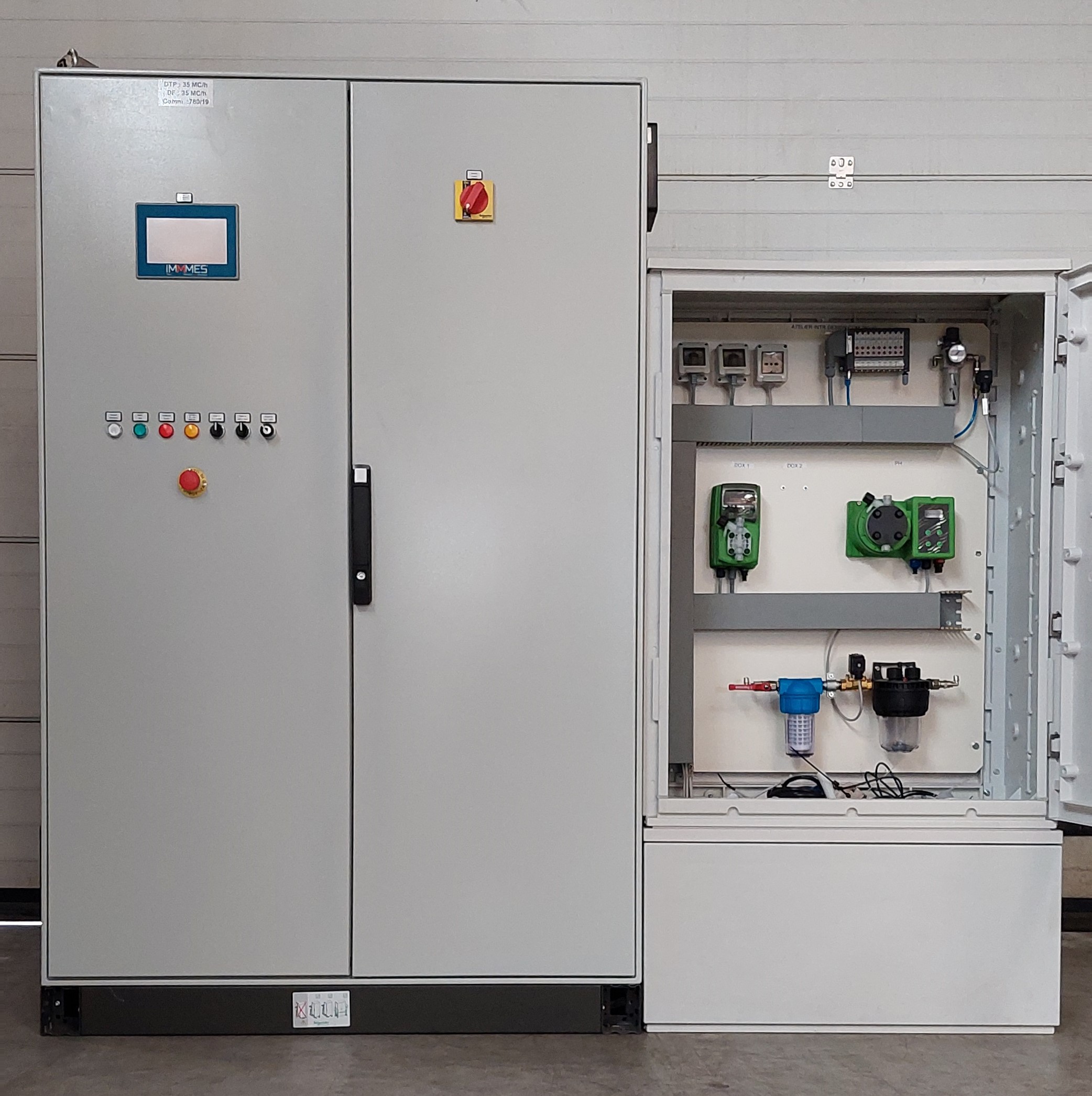
AUTOMATION AND SERVICES
All DTP systems are equipped with high automation in the process and numerous services aimed at facilitating their use and related controls.
A pH station monitors and adjusts the pH value in real time, providing the client the ability to set and maintain an “optimal” level.
Regarding water level maintenance in the circuit, the DTP also offers automatic assistance: an electronic sensor monitors and manages levels in the collection tank. This ensures automatic water replenishment due to evaporation or minor losses during glass handling and production processes.
Similarly, the system automatically handles excess water from external sources such as osmosis plants or rainwater returns to the tank.
Additional services include the ability to program the desired working pressure, remote connection for Immmes teleassistance, and a dedicated remote connection for the client’s use.
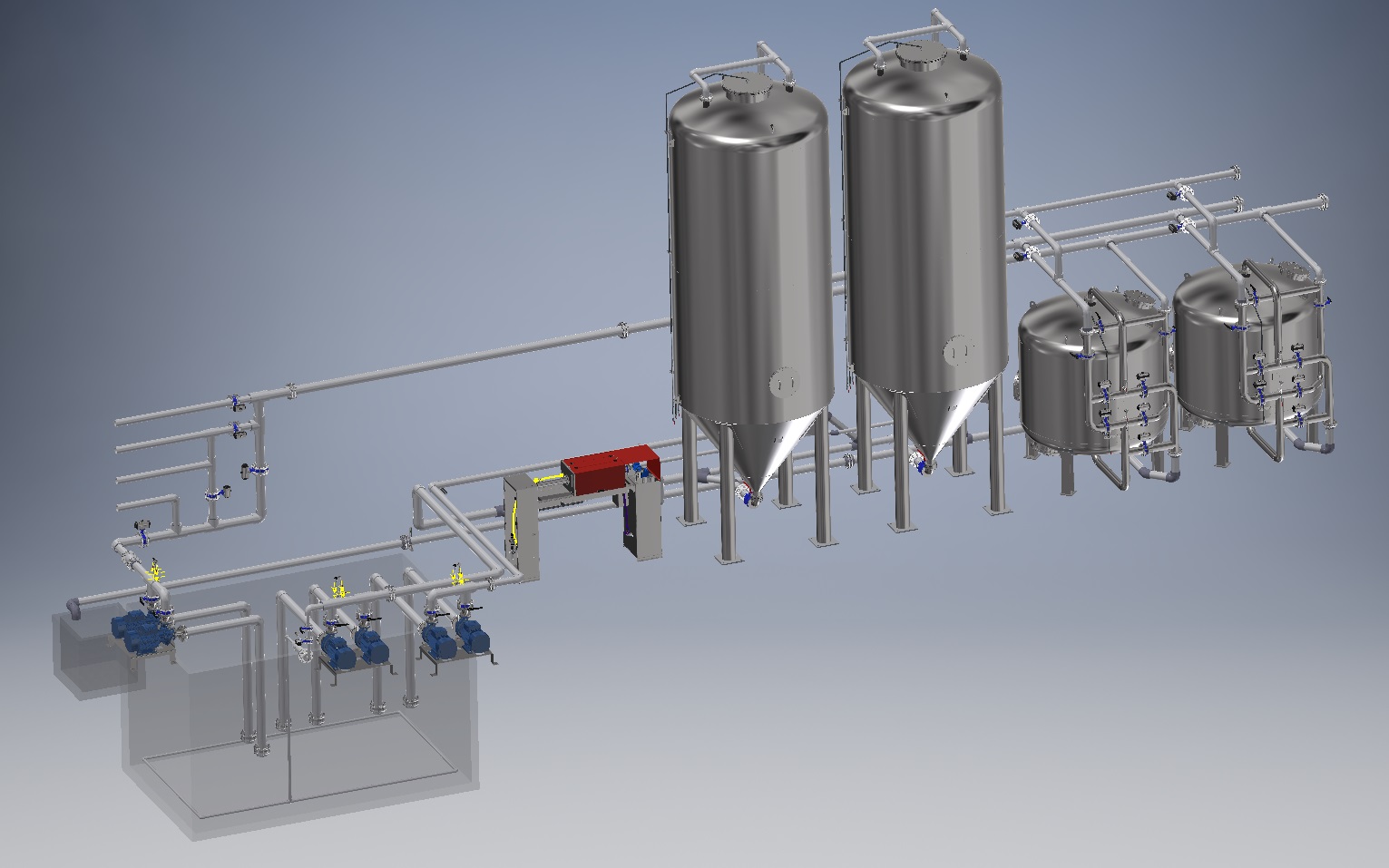
You can cross-reference the information provided above with the DTP advantages chart, aiming to gather the benefits and performances that, we assure you, are unique worldwide.
Upon request, a Business Plan model is available that will allow you to compare the investment and operating costs with your current system or with possible competing options.
ADVANTAGES
Crystal-clear water ideal for use on spindles and washing machines in the production line.
Supply of all required water to the machines for their operation.
Fully automatic operation that does not require an operator.
Remote control for both manufacturer assistance and management monitoring.
Elimination of water tanks under the machines, with the creation of direct drains into channels.
Numerous test points for purification control within the circuit (3 from inside the deconcentrator and 2 from the filter)
45-65% savings on electricity costs due to the elimination of individual machine pumps.
No maintenance required for scaling on machines, tanks, channels, collection tanks, and water transport pipes to the machines.
Optional modules available, such as for 24/7 operation or the creation of any interface for automated production lines.
Elimination of pumps on the machines.
Simple and cost-effective modular expansion of the plant
No use of flocculant products
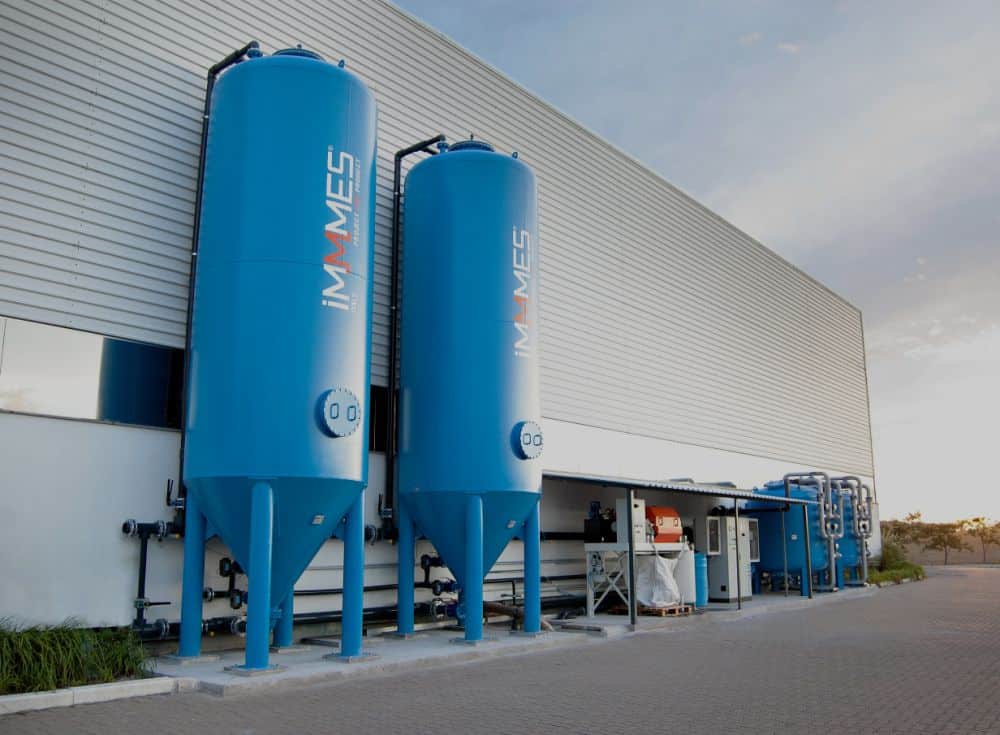
PLANT COMPONENTS
- Dirty water collection tank
- Fluidization system and pump suction units
- Lift pumps
- Deconcentrator
- Sludge deposition system with Big Bags or DGS Filter Press system
- Filter
- Electrical panel and control system
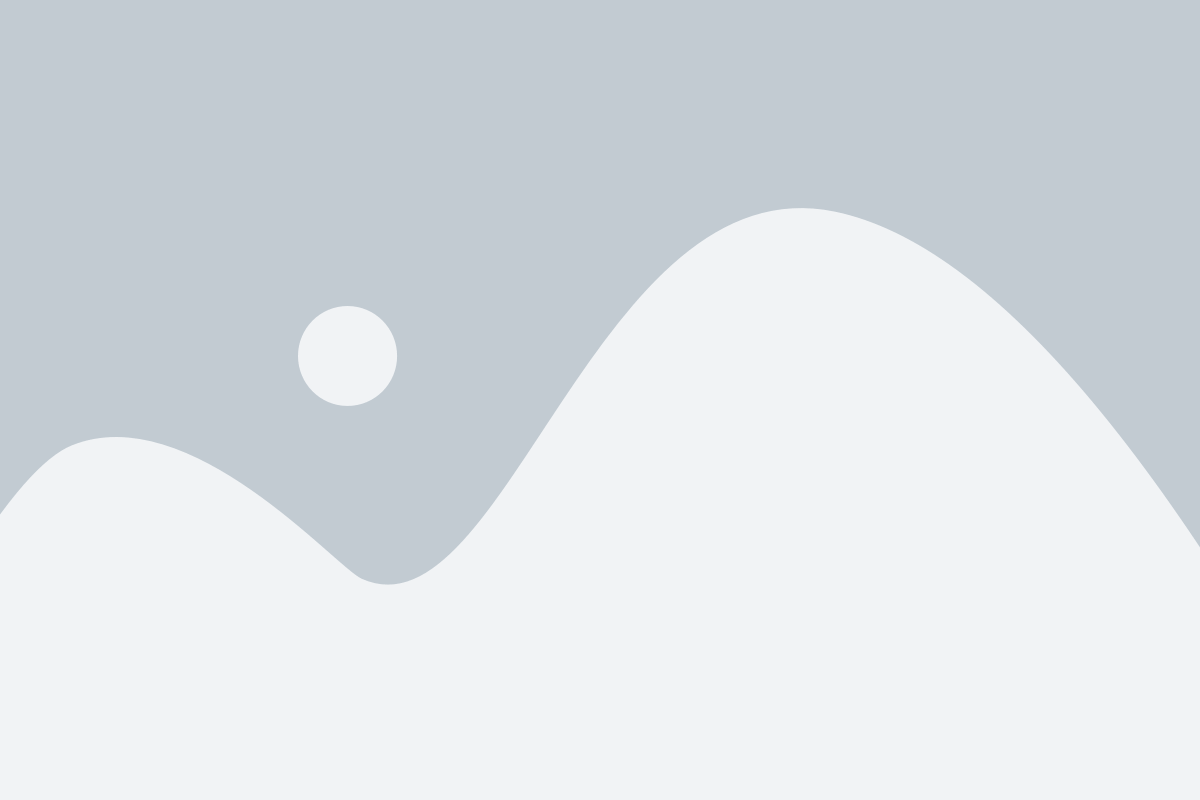
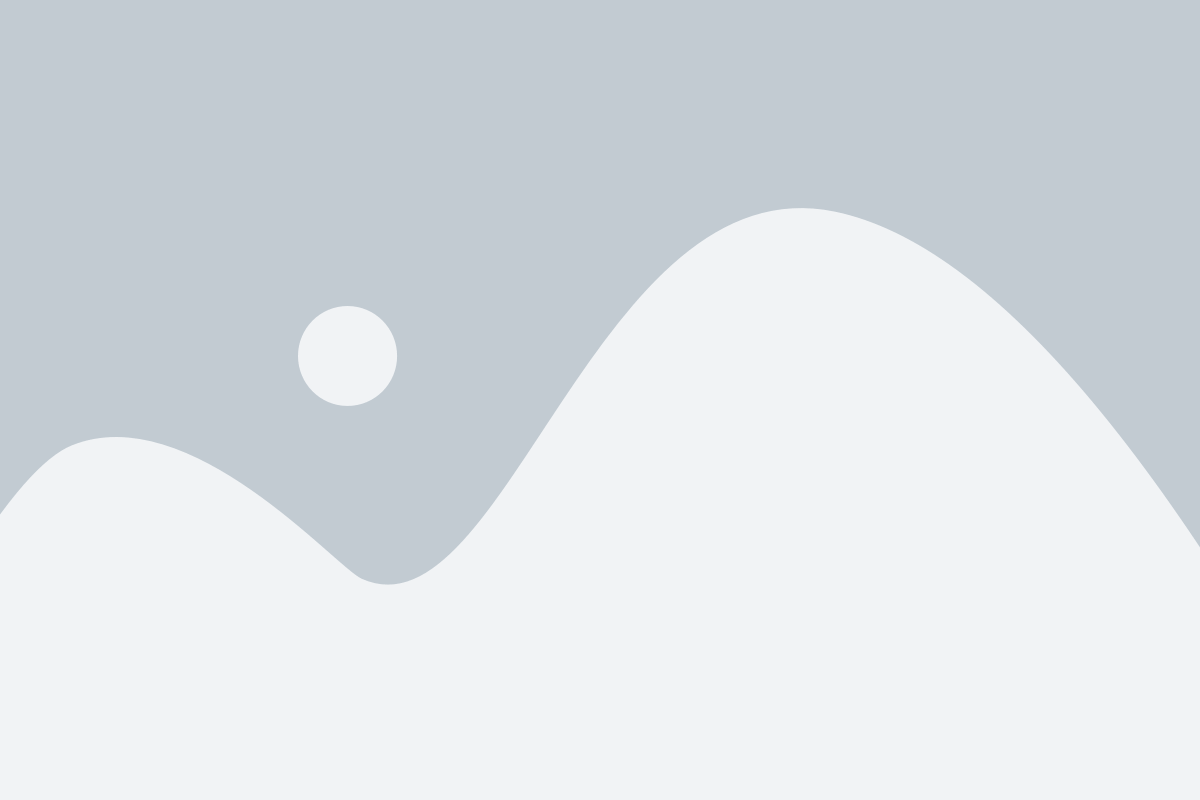
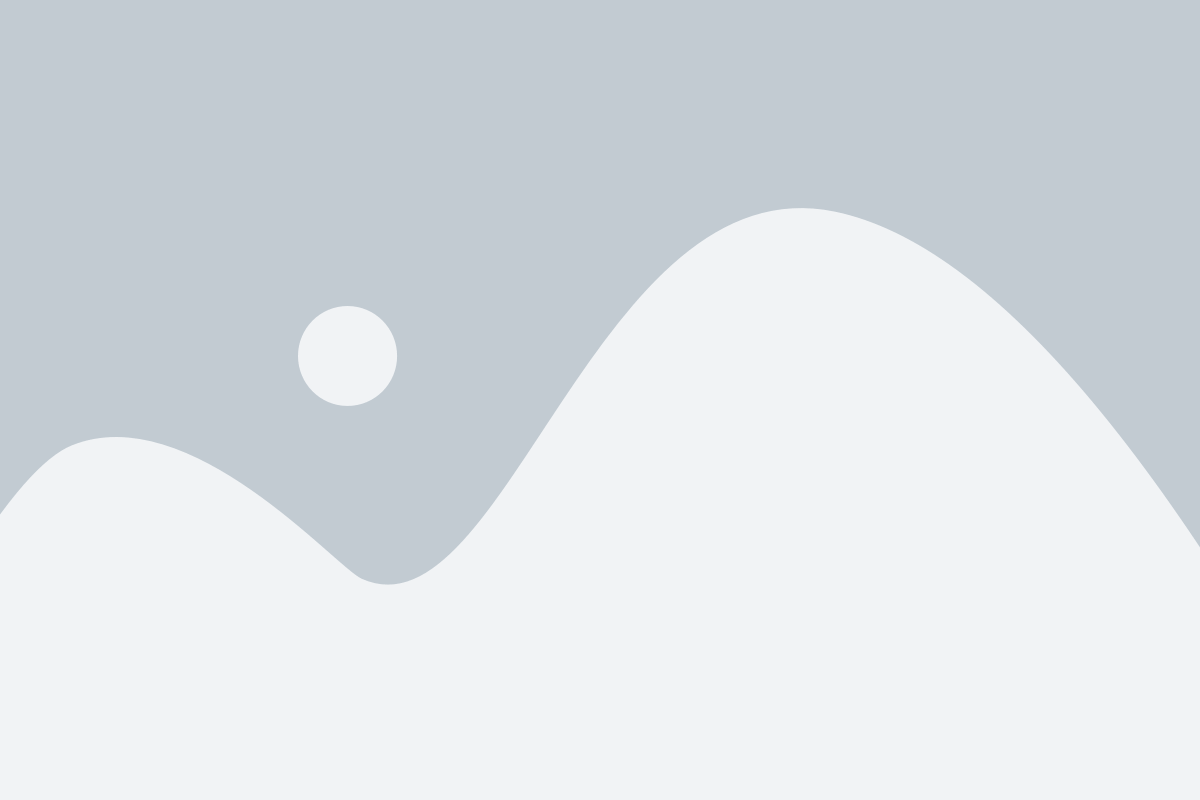